Hesse Mechatronics reorganized the final assembly of wire bonders in its expanded Paderborn production facility according to lean principles and commissioned us to equip the assembly with our LOXrail intra-logistics transport system. Two new flow assembly lines now have an annual capacity to produce about 500 customer-specific wire bonders in different sizes.
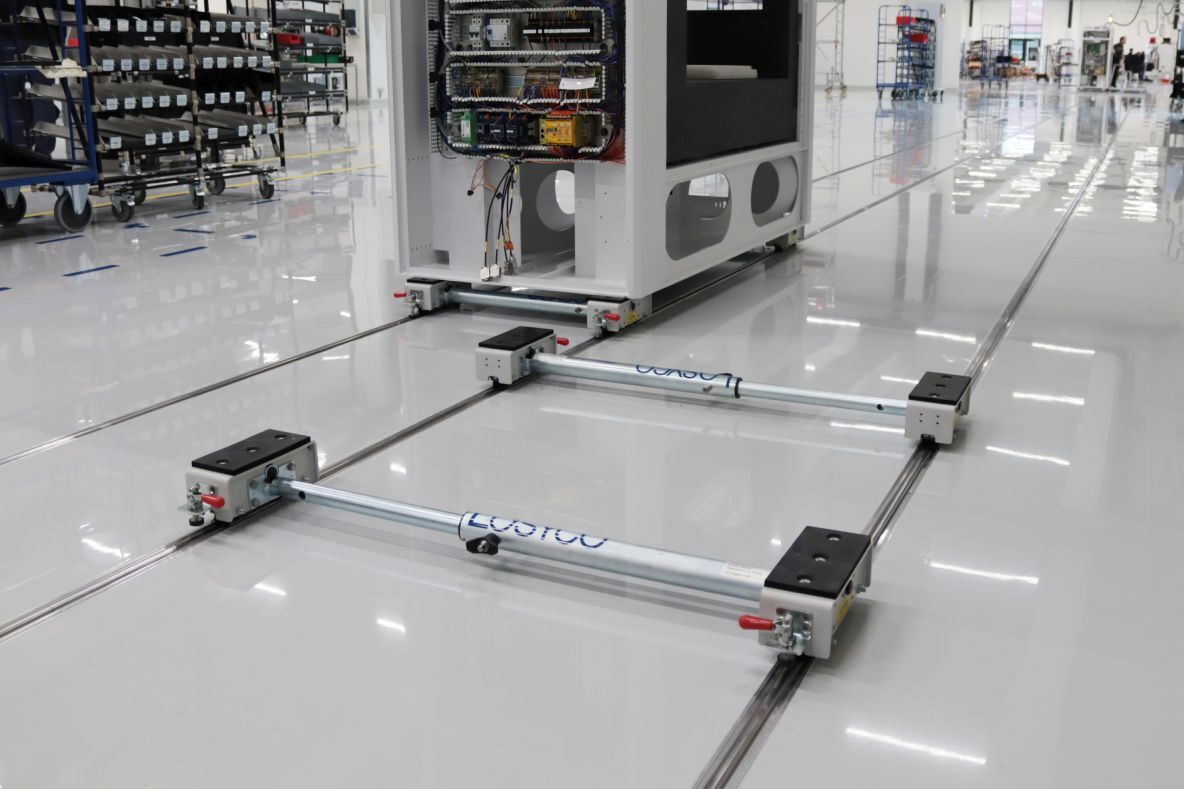
Made-to-measure Bondjet production
Hesse is one of the world’s leading manufacturers of fully automatic machines for packaging and connection technology in the electronics and semiconductor industries. Its portfolio includes the Bondjet series of adaptable machines for thin and thick-wire bonding. The range reaches from compact machines for prototypes and small series production to large-scale wire bonders with large working ranges, high process speed and precision.
Project highlights:
- Floor-level rail installation over a total length of 451 meters
- Flexible assembly line with three different track widths
- Trolleys consisting of two wheelsets connected via a telescopic axis
Production logistics with variable track widths
To enable Hesse to produce all machine types in flow assembly, we laid five rail tracks with a total length of 451 meters in two assembly lines in the plant, which has been expanded by a new hall. First, we installed the tracks in the new production hall. Afterwards, we could extend the tracks for both assembly lines into the existing hall and hand over the completed conveyor system ready for operation. While the first line has two tracks spaced at 650 mm, the second line has three tracks installed at intervals of 650 mm and 1050 mm from each other. This production line therefore offers three track widths for moving differently sized machines precisely from one assembly station – the trolleys for the largest machines can use the full width of 1750 mm.
Width-adjustable trolleys with telescopic axes
We have designed new LOXrail trolleys for the machines, each consisting of two wheelsets with double rollers, which are connected via a telescopic axis in order to be able to adapt the spacing exactly to the track width. Machines are placed directly on two such trolleys, which feature rubberized surfaces and so are optimally equipped to safely carry the load. Workers move the machines by hand. For secure stops at the workstations, each wheelset features a stopper operated via a lever.
This is what the user says:
“It was particularly important to us to have a smooth-running, floor-level system that does not restrict accessibility, on which machines weighing up to 1.8 tons can be moved by hand and securely locked in place. We also attached great importance to a clean and low-maintenance solution. Thirdly, the transport trolleys should be easy to handle and allow for flexible adjustments to different track widths. The cooperation with LOSYCO was excellent from start to finish. The installed rail system has proven itself very well in manufacturing practice.”
Ralf Steffens, COO of Hesse Mechatronics
A German-language case study on this project was published in the trade journal f+h Fördern und Heben, issue 9/2023.